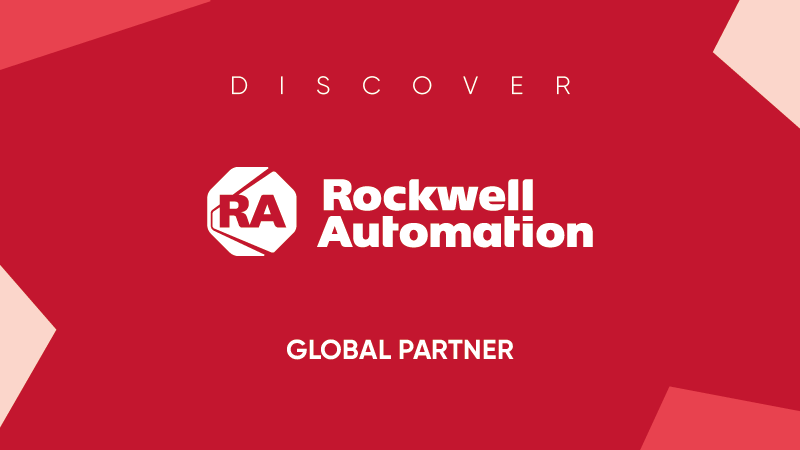
May 10 2022
Modern pressures demand modern answers
The tissue industry is a mirror for many others regarding the market demands and pressures it faces. As a result, the solutions are just as applicable for others… and 100% cemented in digitalization.Like many verticals, the tissue industry is facing a perfect storm of pressures, from numerous actors and across multiple fronts.
Savvy and selective consumers are not only looking for more personalized products, but they are also expecting more choice from standard ranges. And you need to be prepared, as the trends and choices may all change tomorrow!
Choices, skill sets, and sustainability
This expansion of choice and fluctuating trends requires manufacturers to ramp up their SKU count and implement faster development cycles for new lines, while also looking at deploying greater flexibility in existing ones, for seasonal specials, promotional packs or mixed contents. These challenges must be addressed at speed, at scale, and with negligible impact on unit cost.
As is almost always the case, these consumer-driven end-user demands eventually filter down to the machine builders and OEMs, who need to stay at the sharp end of technological development. Some may specialize in vertical markets; others, however, may manufacture machines for other industries too. The primary question here being: “How do OEMs – specialist or otherwise – deliver agility, flexibility, adaptability, and efficiency, at the same speed, scale, and price points affecting their customers?”
Like many, the industry is also seeing the retirement of seasoned engineers and operators, who have an almost intimate relationship with plant and machinery. This tactile approach took years to develop and is impossible to impart or teach to a younger and more multi-skilled workforce, certainly not in today’s shorter timescales. So in among all this new flexibility and agility, we must also factor in ease of use.
Finally, as if these operational pressures were not enough, companies are also facing ever-more stringent environmental legislation concerning energy consumption, green construction, waste and, of course, the materials they use for products and packaging. Indeed, materials development is a real sticking point for many, as new formulations are arriving all the time, all of which can play havoc with finely tuned production parameters.
The key to addressing all of these challenges – as with many contemporary issues – is digitalization, in both hardware and information flow.
Digitalization and data
Modern servo-driven axis control offers almost infinite motion profiles, all of which can be easily programmed, simulated, and enhanced offline before being made available to operators at the push of a button on an HMI. Independent cart technology, including our iTRAK and MagneMotion linear servo solutions, do a similar job with conveying and product transfers.
Properly conceived electromechanical integration can also semi- and fully automate changeover routines, reducing downtime to a fraction of what it used to be. Indeed, machines and lines really do have access to a level of agility only dreamt of a few years back.
At the software level, the most powerful tool, which is now all pervasive in smart manufacturing, is data. Data – from both OT and IT systems – is underpinning the fourth industrial revolution, and its two-way transfer to and from every element of the value chain – device to enterprise – is revolutionizing modern operations.
This data can then be consumed, contextualized, leveraged and/or disbursed by incredibly powerful software systems, such as our Factory Talk Innovation Suite, which includes predictive maintenance capabilities; our Emulate3D Digital Twin software, for virtual commissioning, throughput simulation, and industrial demonstration and dashboards; or analytics through Thingworx, a control system platform that creates a fully smart digitalized production environment.
This bidirectional flow and job-function-specific presentation of essential operational information then allows management to make the right decisions, often in real time and not just during the operational phase. Deployment of this information during design is what slashes lead times and allows companies to hit the market faster. Add virtual commissioning, AR/VR/MR support and training and it is clear to see the value of a digitalized solution.
No digital solution would be complete without cybersecurity, which forms an essential element of any holistic digital package. To this end we have been very active over the past few years with partnership with CISCO and Claroty, and through acquisitions of strategic companies such as Oylo and Avnet, all of which contribute to a multi-faceted cyber solution. This allows us to supply products with specific cyber certification, such as our Logix platform, or to deliver proven network design with our Stratix-based solutions.
See it in action
It's always easy to talk about good solutions. To really get an appreciation of what they can do for you, you need to see them in the flesh, which is why the iT’s Tissue event in Italy is an ideal shopwindow. Described as the unconventional intersection between technology and networking, this unique event gives attendees the opportunity to book and attend half-day experiences at a number of member-company OEMs – in Lucca – where the host companies will support a mix of technical discussion, business development and networking.
As the event’s global partner and exclusive automation supplier, we will have a presence at each of the founding members’ facilities, where we will demonstrate flexible manufacturing, digitalization, analytics, cybersecurity, and workforce connectivity. It really does promise to be a fascinating event, which will really give you an idea of how modern digitalized best practice can open a whole new world of opportunities.
Join us at the iT’s Tissue event in Lucca, Italy, 6-10 June 2022 - register now and enter the future of technology.